Our collaboration
A joint success
As a customer, what can you expect from us? In our family business, communication channels are short and you can rely on your personal contact person to work with you to find solutions for your individual requirements. Our cooperation is based on mutual appreciation and trust in each other's expertise. You can find an overview of the processes from the first contact to the finished system here:
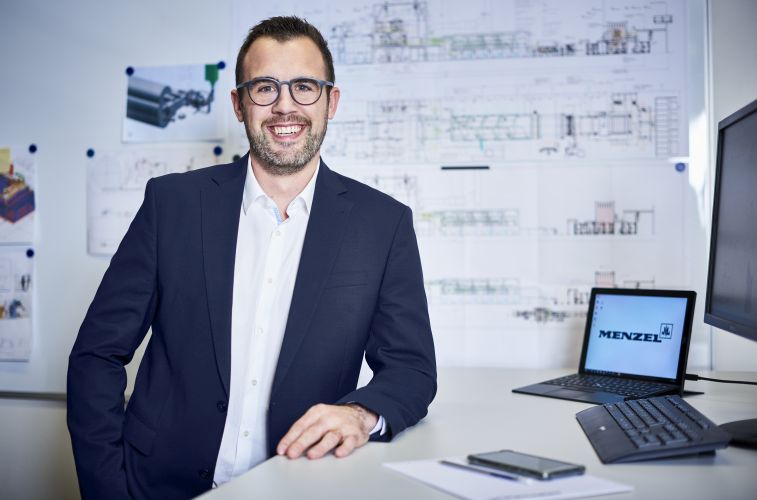
Our first contact
Welcome! You came to us because you need a machine to wrap, coat or finish film, nonwovens or technical textiles? Do you have very individual requirements? Or do you have an idea for a special product that places unique demands on production? You can get in touch with us here.
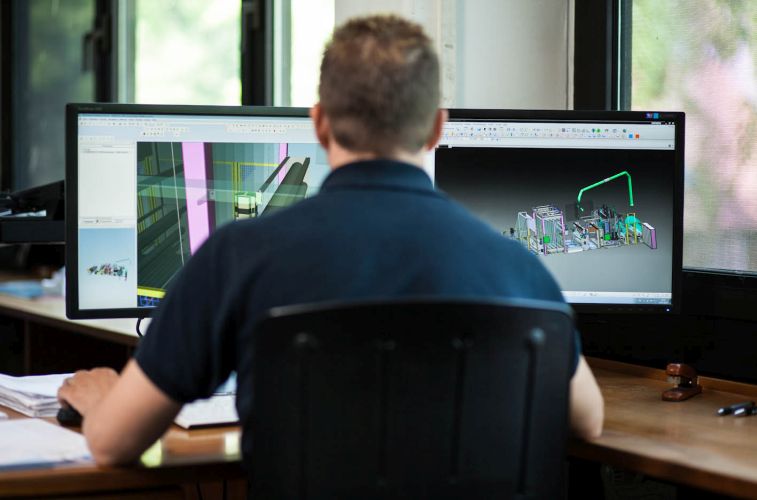
The idea
Our sales and engineering staff will advise you on the feasibility and approximate cost of your project. In close consultation with our customers we develop a machine design based on your wishes and requirements. You will then receive our quotation for your individual Menzel machine.
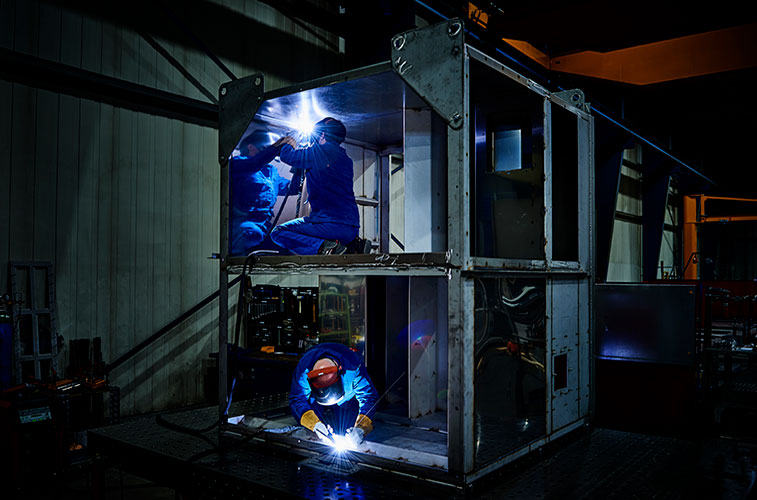
Production
Your Menzel machine is manufactured at our plants in Bielefeld and Schloß Holte-Stukenbrock. Our very high level of vertical integration enables us to cover the entire process chain from a single source. The highest quality standards are the benchmark for the individual production steps.
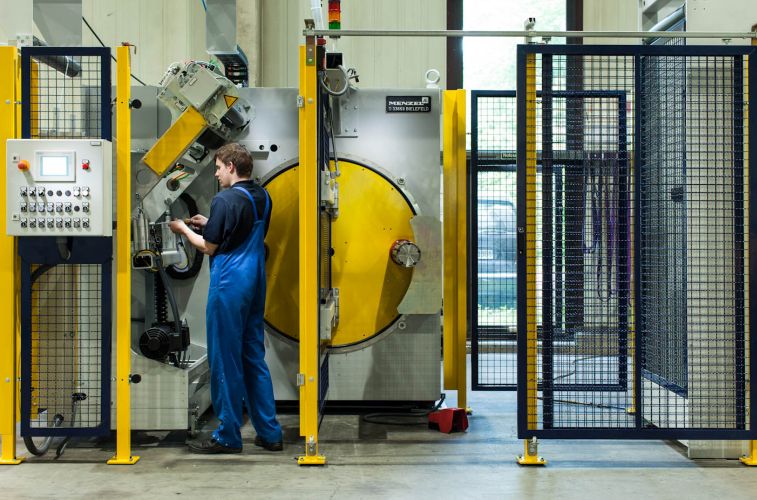
Assembly
Each system is fully assembled in our factory by our assembly teams before delivery. We can test the machines in production-like conditions in our spacious assembly halls. This guarantees our customers functional reliability and short on-site installation and commissioning times.
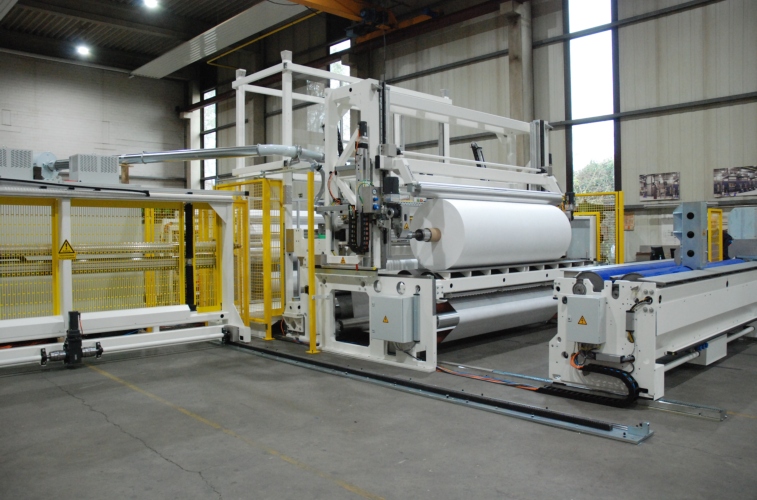
Factory Acceptance Test
After your Menzel machine has been set up and tested at our factory, we will carry out the Factory Acceptance Test (FAT) together. This allows you to check the machine in detail.
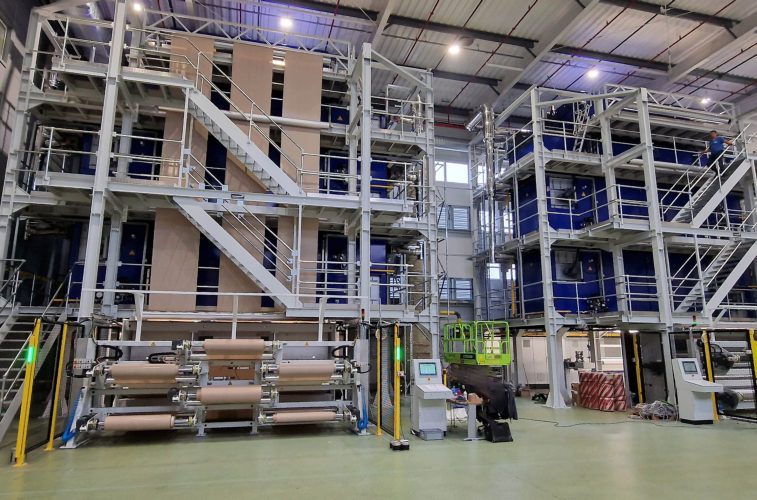
To the finished plant
The machine is then dismantled, transported to the customer and reassembled by Menzel fitters. The system is then commissioned by our electricians. During this time, your operators can also be trained; optional training after handover is also possible.
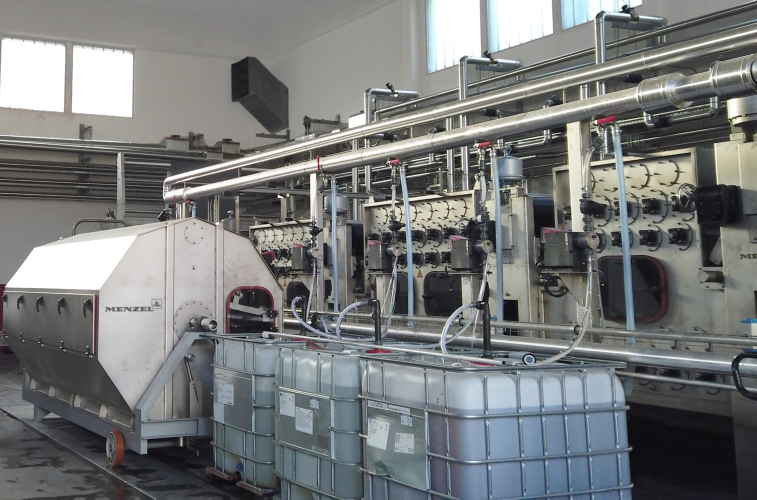
Final acceptance
Once commissioning is complete, we carry out a final acceptance test with you. This includes a safety test and a test run with the product. You will receive the documentation (instruction manual, spare parts list, data sheets).
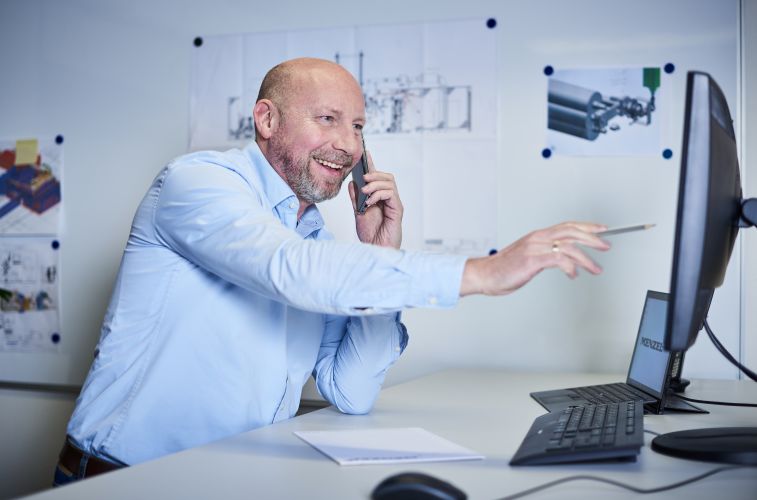
Service
Of course, our service is available to you throughout the entire process. And beyond! Your Menzel machine is supported by our maintenance and spare parts service throughout its entire long life cycle.
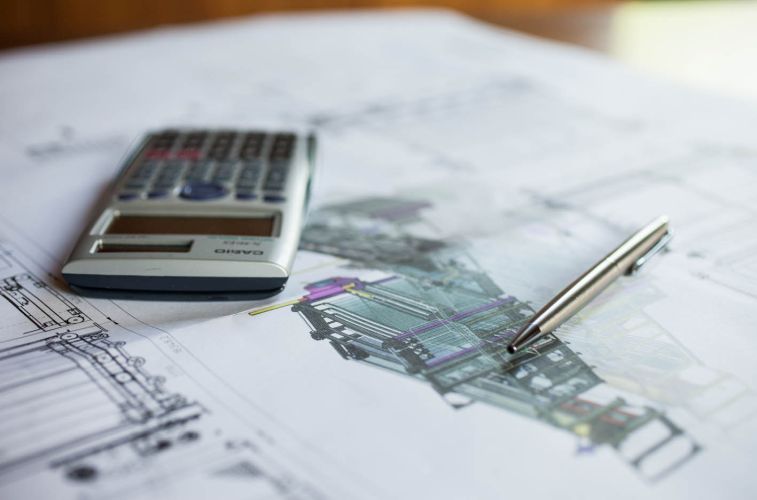
And beyond!
Even after the project is complete, we continue to work with our customers: The modular design of our systems and the possibility of further development make our machines future-proof in your company!
We realize YOUR project!
Do you need more information? We look forward to hearing from you!